40 年以来,板状刚玉已广泛应用于钢铁、铸造、石化和陶瓷用高性能耐火材料。板状刚玉因其高的耐火度、优异的抗热震性、抗蠕变性和耐磨性,而成为主导的合成高纯氧化铝骨料。尽管耐火材料的整体消耗量急剧下降,尤其是在钢铁制造上的应用,但是板状刚玉的使用不仅相对增长了,而且是绝对增长了。连铸的引入,不定形耐火材料比例的稳定增加,以及优质钢的猛烈趋势都是板状刚玉基耐火材料发展的动力。本文的目的是描述板状刚玉的典型性能,与其他合成高铝骨料相比结果怎样,以及它的典型应用。也会介绍板状刚玉与尖晶石和无钙结合剂共同使用的最新进展。
2 性能
板状刚玉是致密的、完全收缩的、烧结的α-al2o3,由 50-400μm 的晶粒构成骨料结构。板状刚玉因其晶粒形状像板子而得名。在稍低于熔融温度下快速煅烧超细α-al2o3 料球制备板状刚玉。热处理后,破碎或碾磨 18-20mm 的料球得到各种尺寸的板状刚玉,见表 1a。
表 1a 常见的板状刚玉尺寸
表 1b 总结了板状刚玉的性能。看它的化学组分,高纯是很重要的,典型的氧化铝含量大于 99.4%。氧化铝有粗颗粒,也有小至-325 目(等于公制的-44μm)的细粉。板状刚玉的主要杂质是氧化钠,典型值是0.2-0.4%。
对于优异的高温性能来说,刚玉中氧化硅、氧化铁和氧化钛的低含量是非常重要的。溶酸铁的超低含量(典型值是小于 0.002%)对于磷酸盐结合耐火材料是非常重要的。对比烧结板状刚玉和其他合成高铝骨料,例如电熔白刚玉,发现最大的差别在于具有较细尺寸的杂质含量。这会引起巨大的性能差异,尤其是高温性能。较高的杂质含量以较细的尺寸引入,会大大降低高温体积稳定性和抗蠕变性。
对比电熔白刚玉和板状刚玉的气孔率,能看到巨大的差异。尽管两种骨料的总气孔率一样,但晶粒气孔有显著差别。
电熔晶粒的开口气孔率是烧结晶粒的 2-3 倍。电熔氧化铝的大部分气孔由大的开口气孔构成,而板状刚玉有超过一半的气孔是闭口气孔。高比例的闭口气孔对于高的抗热震性是很必要的,这是板状刚玉的典型特征。图 1 和图 2 是热震试验结果,挑选尺寸为 5mm,接近等轴的 300 个晶粒来进行试验。300 个晶粒等分为三份,分别在 20℃和 1300℃之间进行热循环 10 次、20 次和 30 次,记录未破坏的颗粒数。从未破坏颗粒中选择 30 个,测量耐压强度。从这个试验观察到了烧结刚玉和电熔刚玉之间的很有意思的差别。板状刚玉表现出高的抗热震性和高的强度。扫描电镜照片显示板状刚玉晶粒表面不像电熔刚玉晶粒的表面那样光滑,比较粗糙,有浅的半球形气孔。这种表面结构促进了它与基质的反应和机械互锁,从而提高了耐火材料的强度。
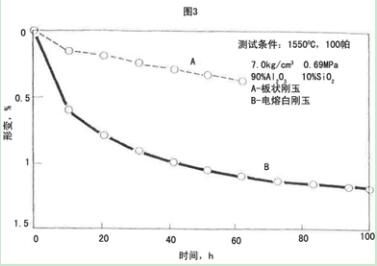
低的开口气孔率和 2-3 倍高的闭气孔率;
高的颗粒堆积密度,3.55-3.6g/cm3;
高熔点>2000℃;化学惰性;好的抗热震性;
优异的体积稳定性;
3 板状刚玉的主要应用领域
上述的板状刚玉的性能在耐火材料领域的有许多应用。主要应用于钢铁工业。板状刚玉是高铝砖和不定形衬的含 90-100%氧化铝的理想材料。表 3 列出了板状刚玉的主要应用领域。板状刚玉适用于陶瓷、化学和水结合基质。板状刚玉可以单独和结合系统使用,也可以和煅烧和/或活性氧化铝一起使用。因为板状刚玉,即使是细粉,也表现出极高的纯度,所以它可以用来提高较低氧化铝骨料的性能,例如铝矾土和电熔棕刚玉,使用这些骨料的粗颗粒和板状刚玉的中颗粒和细粉。前面已经提到过,板状刚玉消耗的增加主要来自于钢铁的连铸。尤其对于滑板、浸渍管和水口,使用板状刚玉是工业标准的要求。
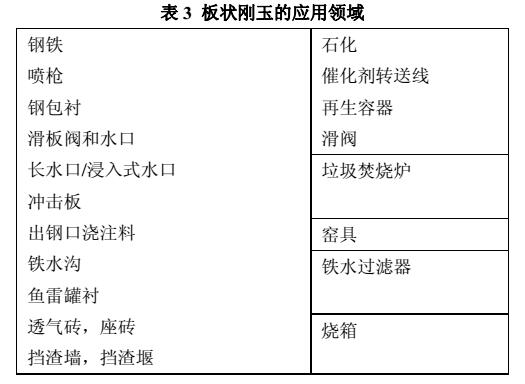
日本已经发现向水泥结合板状刚玉耐火材料中加入 20-30%的富铝尖晶石能显著提高抗渣侵蚀性。因为富铝尖晶石在全球非常普遍[4],这一概念引起了板状刚玉更多新的应用。尤其是钢包的不定形衬促使了板状刚玉在未来的使用。最近发表的文献[5]表明,尖晶石能把水泥结合的水泥板状刚玉浇注料在 1500℃ 下的热态抗折强度提高到 22 n/mm2。要注意到很重要的一点,即使使用 15%的水泥也没有降低高温性能。考虑到水泥含量较低的浇注料的高温抗折强度会降低一个量级,不能看出这些发现会对未来的耐火材料技术产生很大的影响。可能能使用一些浇注料,它的水泥含量较高且热态性能高于超低水泥浇注料,还没有 ulcc 已知的可重复性的缺点。有趣的是在尖晶石板状刚玉浇注料中加入 2%的硅微粉就能使 1500℃下的热态抗折强度降低到 1 n/mm2 以下。
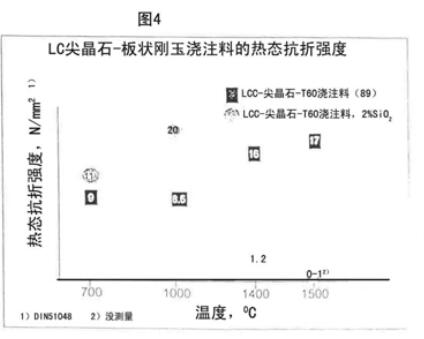
因为水泥结合氧化铝系统在富二氧化硅的渣环境下有一些局限性,所以开发了纯氧化铝基结合剂的alphabond 系统。主要化学组分是氧化铝,含有杂质 cao(0.1%)、sio2(0.2%)、na2o(0.5%)和水(≤9)。它可以像普通的铝酸钙水泥来对待。这个系统可以单独使用,也可以和硅微粉一起使用。表 4 是 alphabond 结合的浇注料和相似的水泥结合浇注料的性能的对比。
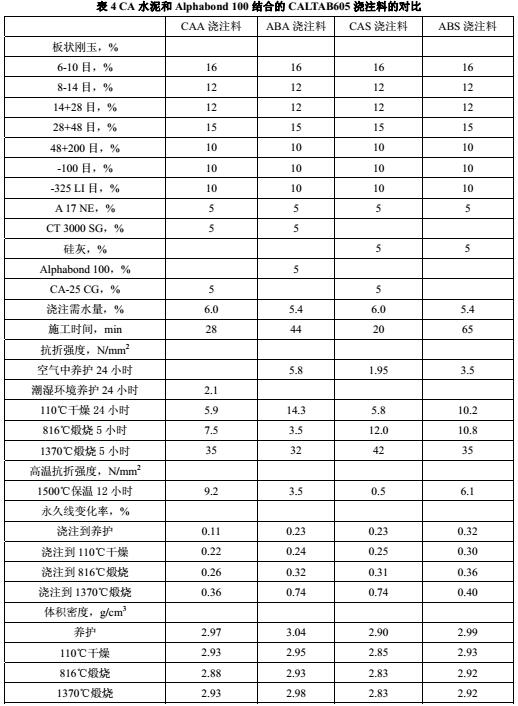